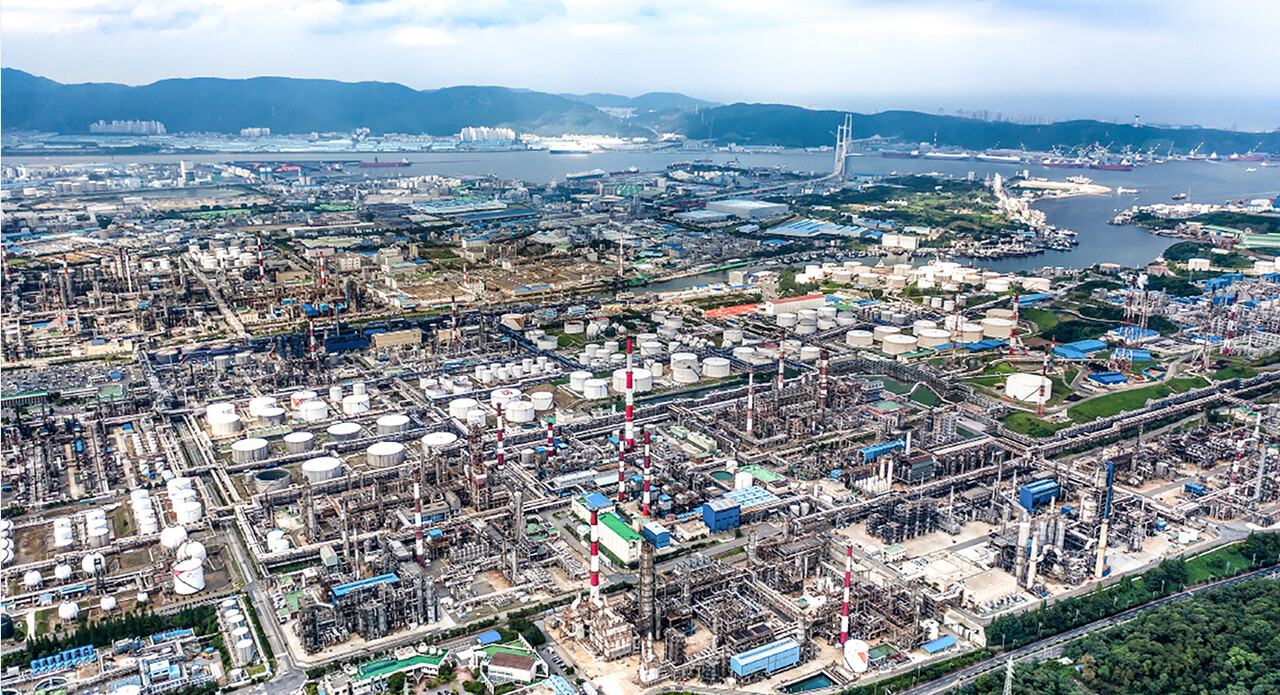
[울산=데일리임팩트 김현일 기자] SK이노베이션의 심장, 울산컴플렉스(Complex, 이하 CLX)에 스마트한 맛이 가미되고 있다. 지난 2016년 스마트 플랜트 개념을 업계 최초로 도입한 데 이어 2023년에는 이를 ‘스마트 플랜트 2.0’으로 업그레이드하며 한 단계 높은 수준의 인공지능(AI)·디지털 트랜스포메이션(DT, 디지털 전환) 기술을 선보이고 있기 때문.
비록 아직은 걸음마를 떼는 단계라 기술이 과거 ‘2G폰’ 정도 수준이라는 것이 이들의 입장이지만, 기술이 점점 발전하고 있는 데다 이를 외부 업계에 판매하는 작업 역시 진행 중인 만큼 향후 스마트 플랜트 분야에서는 물론, 산업혁명 4.0 시대를 선도할 가능성도 충분히 있어 보인다.
지난 23일 기자단은 울산광역시 남구 SK울산CLX에 다녀왔다. 이곳에서는 해외에서 들여온 원유를 정제해 휘발유를 비롯해 등유·경유 등의 석유제품, 윤활유·잉크·아스팔트·폴리프로필렌(플라스틱의 일종) 등 총 680종의 석유화학 제품을 생산하고 있다.
환갑 맞은 거대 단지… “그래도 속은 건강해요”
울산CLX는 여의도 면적의 3배가 넘는 826만m2(제곱미터, 약 250만평)으로, SK이노베이션뿐 아니라 SK에너지·SK종합화학·SK루브리컨츠 4개 회사가 입주해 각종 △정유 △석유화학 △열병합 발전소 등을 운영하며 하나의 단지(컴플렉스)를 형성하고 있다. 그 크기가 거대한 만큼 내부 이동 시에 버스를 타고 움직였는데, 아직 깔끔한 신시설도 있었으나 갈색으로 녹이 슬어있는 구시설들이 어우러져 있어 이 시설이 버텨온 고된 세월을 짐작케 했다.
심지어 1964년 처음 지어질 당시의 공장도 여전히 현역이라는 점에서 한 편으로는 그 내구성이 염려되기도 했으나 안전성에는 전혀 문제가 없다는 것이 관계자의 설명. 도색을 하는 것도 고려했지만, 탱크 1개를 칠하는 데에 약 10억원이 드는 만큼 비용 문제도 만만치 않아 현재의 모습을 유지하기로 했다고 한다.
박지혜 SK에너지 CLX대외협력팀 PM은 “환갑이 지난 공장이지만 여전히 가동을 하고 있고, 그 대신 내부에 있는 모든 설비나 리액터들은 전부 다 교체가 된 상태다. 그래서 겉모습은 조금 오래돼 보일 수 있겠지만 내부는 거의 새것과 같다고 보면 된다”라며 “정유 산업이 대체적으로 바깥으로 드러나는 산업이라 비나 눈이 오면 겉으로는 녹이 슨다. 겉으로는 운영에 문제가 있는 건 아닌가 싶기도 하겠으나 항상 두께를 체크하고, 정비시간도 갖고 있어 안전상으로는 큰 문제가 없다”라고 설명했다.
공장 곳곳에 다양한 형태로 뻗어 있는 파이프라인도 인상적이었는데, 이 내부를 따라 원유가 이동하면서 공장들로 이동하며 작업이 이뤄진다고 한다. 형태가 일자로만 곧지 않고 ㄷ(디귿)자, ㄴ(니은)자로 다양했는데, 석유화학 제품이 흐르는 철제 파이프가 겨울과 여름을 거치며 수축과 팽창을 반복, 점차 균열이 생길 가능성이 있어 완충작용을 한 것이라고. 이를 모두 이으면 무려 60만Km(킬로미터)가량으로, 단일 공장을 기준으로 세계 최장 거리임은 물론, 울산에서 달까지 갔다가 절반가량 돌아올 수 있는 길이라고 한다.
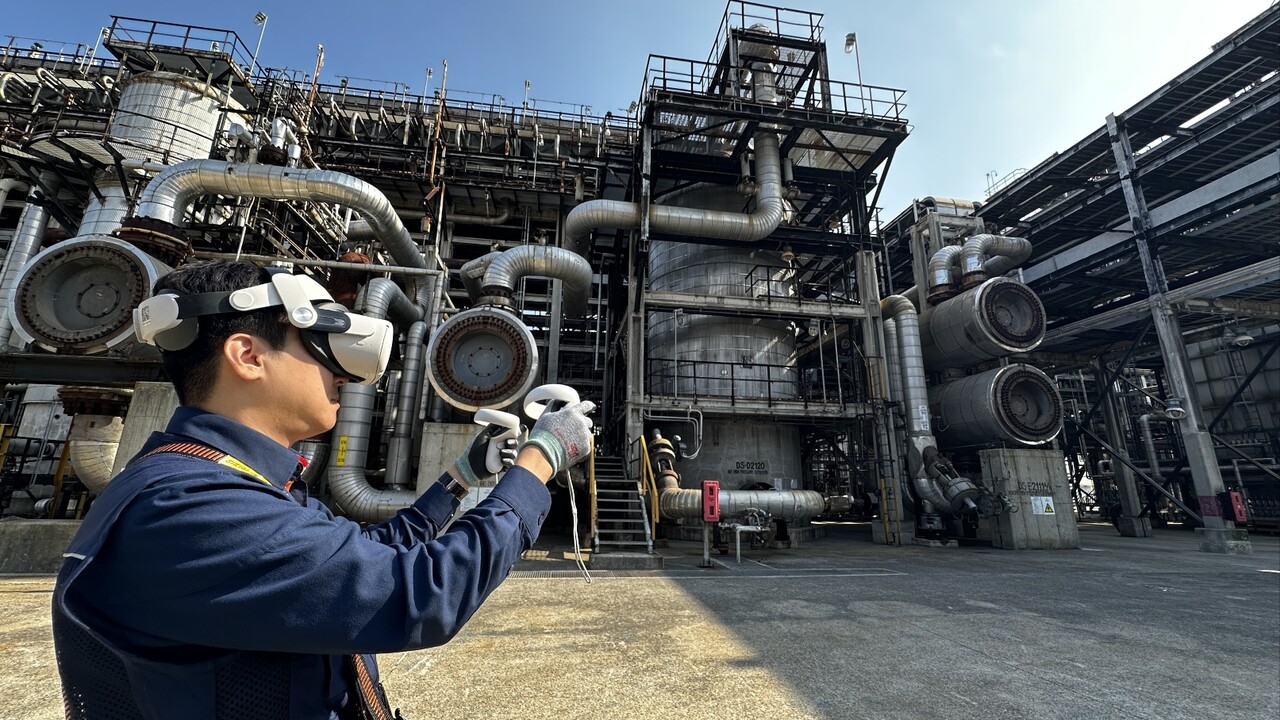
‘아니, 공장에 일하는 사람이 이렇게 없어도 되나?’
특이했던 점은 그 넓은 공장 지역 내부를 돌아다니는 동안 직원들을 거의 볼 수 없었다는 점이었다. SK이노베이션 측에 따르면 모든 정유 공장이 전부 자동화 시스템을 갖추고 있다 보니 밸브를 여닫거나 보수하는 작업 등도 전부 조정실에서 직원들이 진행하고 있어 외부에서 근무를 하는 이들이 별로 없다고.
이는 SK이노베이션이 울산CLX에 적용한 스마트 플랜트 개념 덕분인데, 일반 제조업의 스마트 팩토리와는 달리 석유/화학 산업 특성을 고려한 디지털 전환의 개념이다.
SK 울산CLX는 지난 2016년 스마트 플랜트를 업계 최초 도입한 현장으로, OASIS(생산관리), OCEAN-H(설비관리) 등 데이터 및 업무 관리에 대한 기간 시스템을 구축해 디지털 트랜스포메이션(DT) 추진 기반을 확보했다. 이 기간 시스템을 통해 확보한 데이터를 기반으로 AI 개발 및 적용에 속도를 내고 있다.
2019년부터는 스마트 플랜트 2.0을 본격적으로 추진해 지난 2023년부터 공정 운전, 설비 관리, SHE(안전/보건/환경) 분야에 AI와 DT를 적용한 40여개 과제를 SK 울산CLX에 적용하고 있다. 주요 과제로는 △공정 자동 운전 프로그램 △공정 자동 제어 고도화 △설비 고장예측 솔루션 △울산CLX 통합 안전 모니터링 체계 구축 등이다. 업무 자동화 및 지능화 기술을 도입해 에너지 절감, 생산성 향상 등을 통한 비용 경쟁력을 높이고 사고 및 설비 고장을 예방하는 안전성까지 확보하는 것이 핵심이다.
이미 개발된 국내외 솔루션이 아닌 현장 상황에 맞춰 자체적으로 개발된 시스템이 다수 도입돼 있다는 점도 SK 울산CLX의 특징. 외부 업체의 솔루션은 현장 적용에 어려움이 발생하는 경우가 잦았던 만큼 기술적으로는 부족할지언정, 스스로에게 맞는 프로그램을 직접 만들어 현장 적용의 어려움 등을 극복했다는 것이 관계자의 설명이다.
예를 들어 서양 업체의 솔루션은 전체를 조망하는 데에 익숙한 동양인들과 달리 부분을 보는 데에 집중하는 사고방식이 시스템에 녹아있어 문화적 차이를 크게 느끼기도 했다고.
정창훈 SK에너지 스마트플랜트 추진팀장은 “(외부 솔루션을) 도입하는 경우도 있으나 보통 IT(정보통신) 회사는 IT만 알 뿐, 우리가 뭘 원하는지 정확히는 알지 못한다. ‘이렇게 만들어주세요’ 하면 (결과물을) 받았을 때 막상 쓰려면 ‘이게 아닌데… 다른데…’ 싶은 게 있어서 시스템을 못 쓰게 되고, 그래서 시스템이 사장되는 경우도 있다”라며 “직접적으로 (기술 개발을) 하다 보면 저희가 (솔루션) 기술은 좀 떨어질지언정 결과물들이 훨씬 현장에서 유용하게 활용이 가능한 경우가 많다”라고 말했다.
이외에도 갑작스러운 인력 누수에 대처하는 것 역시 스마트 플랜트 도입 기대 효과 중 하나. 관계자에 따르면 과거 일본 화학 플랜트 업계에서는 제2차 세계대전 이후 ‘베이비붐’ 당시 태어난 ‘단카이 세대(1947년~1949년, 단카이는 일본어로 ‘덩어리’)가 은퇴할 당시 인력들의 숙련도가 급격히 떨어지며 사고가 2배 증가했던 사례가 있다고 하는데, 이와 같은 역량 누수 사태가 발생하지 않도록 데이터화·디지털화를 진행하는 중이라고.
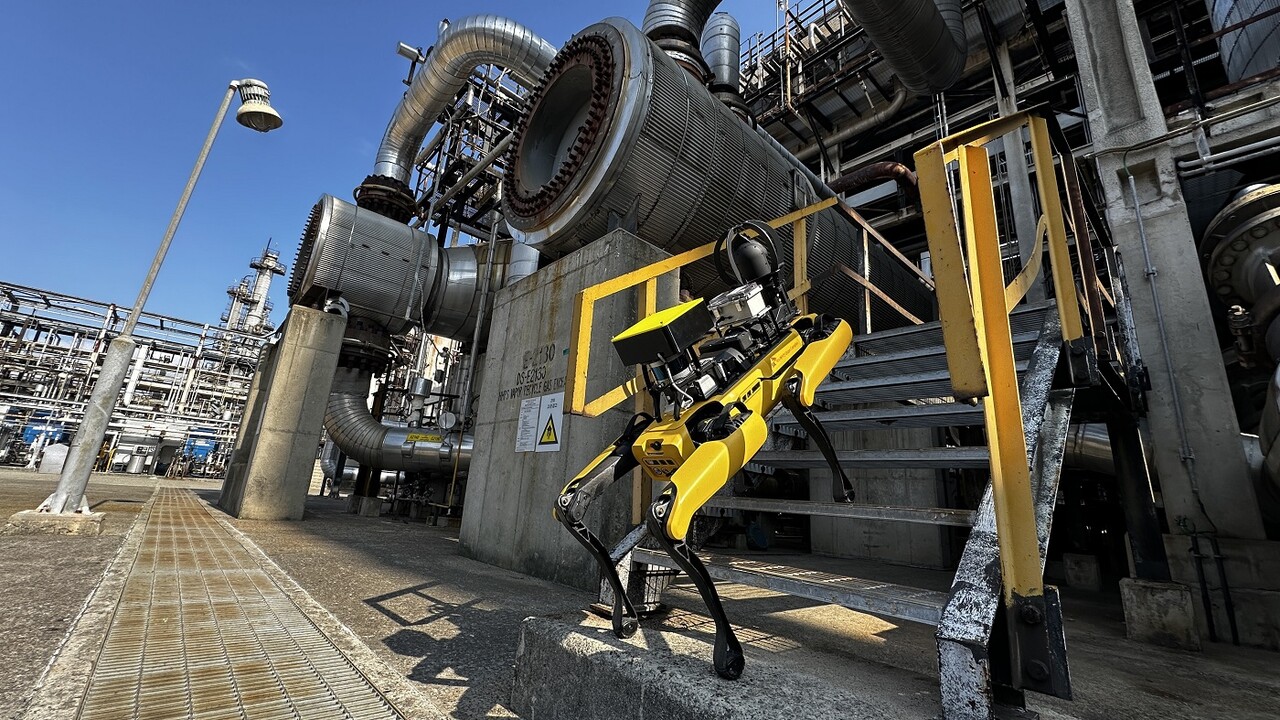
현장 관리하는 로봇 개… 생각보다 일 열심히 한다
이날 가장 큰 볼거리 중 하나는 가스 누출 감시, 게이지 측정 등의 업무를 수행하기 위해 국내 정유사 최초로 도입된 ‘로봇 개‘였다. 이는 현대자동차그룹 산하의 로봇 기업 ‘보스턴 다이내믹스’ 사의 제품으로, 지난 2022년 세계 최대 가전제품 박람회인 CES에서 정의선 회장과 함께 등장하며 화제를 모으기도 했다.
다만 이날은 시설을 주의 깊게 들여다보며 업무를 열심히 수행하고 있어 공장 내를 활보하는 모습을 볼 수는 없었다는 점에서 아쉬움이 남기도 했다.
로봇 개는 설정해 놓은 경로와 미션 스케줄에 따라 자동으로 돌아다니며 △가스 감지기 △열화상 카메라 △30배 줌 카메라 등 설치된 장치들을 기반으로 공장의 이상을 감지한다. 자동차의 ‘크루즈 컨트롤’에 해당하는 자동 회피 기능도 탑재해 사람의 도움 없이 혼자 돌아다니는 것이 가능한데, 사람이 현장에서 놓치고 지나치는 것들을 보완해 줄 수 있는 역할을 할 수 있다고. 1회에 40~50분씩, 하루에 6번씩 순찰하는데, 순찰이 한 번 끝나면 다시 ‘개집’으로 돌아가 충전을 진행한다.
현장에서 만난 관계자는 “로봇 개가 공장관리를 너무 잘해서 리크(leak, 기름 유출)가 없다. (결함이) 있는데 못 찾은 사례는 없다. 개가 없을 때에는 오퍼레이터 운전원 분들이 순찰을 하신다”라며 “(로봇 개 도입으로 인한) 일자리 감소 효과는 당장은 없을 것이다. 사람이 하루 세 번 (순찰을) 할 걸 4~5번 할 수도 있고, 야간에도 할 수 있다”라고 설명했다.
SK이노베이션은 로봇 개를 테스트하는 한편 이에 적합한 여러 비전 AI 기능도 개발 중이며, 시스템이 정착되면 단계적으로 도입 범위를 확대해 나갈 예정이라고 한다. 현재 로봇 개는 울산CLX 내 일부 공정에만 적용돼 있으며, 안전 문제를 이유로 현재 야간에는 순찰을 하고 있지 않지만 주간 테스트가 성공적으로 마무리될 경우 올 하반기부터는 야간 순찰에 투입하는 것도 고려 중이라고.
또한 드론을 공중에 띄워서 작업을 하기도 하는데, 사람이 올라가지 않고 원유 저장탱크 상부에 균열이 생겼는지의 여부도 확인할 수 있었다. 항공촬영을 통해 확보한 도면을 평면상에서 관리해 넓은 곳을 관리하는 데에 있어도 이점이 많아 보였다.
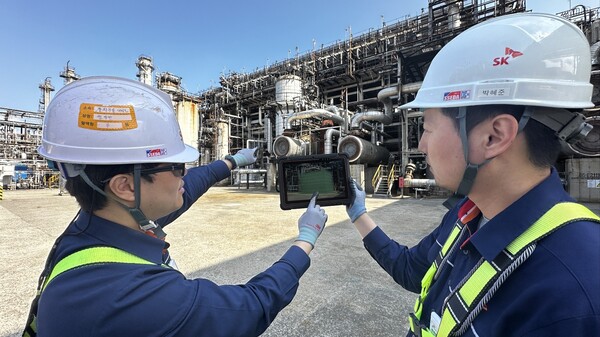
VR·AR 효과도 쏠쏠… 사업화도 착착
이외에도 지난 1월 도입됐다는 증강현실(AR, Augmented Reality)을 활용한 가상에서의 비계 설치 작업 역시 인상적이었다. ‘비계’란 건축공사 시 높은 곳에서 일할 수 있도록 설치하는 임시 가설물로, 높은 길이의 탱크들이 즐비한 울산CLX와 같은 현장에서의 작업을 위해서는 필수적인 장비다. 해당 시스템은 로봇 개를 통해 분석한 데이터를 기반으로 작동한다.
태블릿 PC를 든 작업자가 카메라로 시설을 비추자 AR 시스템이 초록색으로 가상 비계를 어디에 설치할지 실제 현장에 입혀서 보여주는 것을 확인할 수 있었다.
물론 신기하기도 했지만, 비계를 실제로 설치하기 이전에 미리 작업 결과를 확인할 수 있다는 점에서 해당 시스템은 매우 유용해 보였다. 직접 치수를 재거나 하지 않아도 될뿐더러, 비계 수를 늘리거나 줄여 현장별로 최적화된 세팅이 가능해 상당한 비용 절감 효과가 기대되는 부분이었다.
그리고 이러한 현장 작업을 하기 이전에 가상현실(VR, Virtual Reality) 작업을 진행함에 따라 위험한 현장에서의 AR 작업을 진행하는 데에 대한 부담도 적다고 한다. 또 정보 데이터를 미리 쌓아놔서 새로운 작업자가 오더라도 업무 인수인계에 큰 어려움이 없다는 것이 이들의 설명.
앞으로 SK이노베이션은 이러한 스마트 플랜트 2.0 시스템의 활성화를 통해 연간 100억원 이상의 비용 개선 효과를 기대하고 있다. 아울러 자체 구축한 솔루션의 지식 자산화를 통해 새로운 사업모델로도 확장할 계획이다.
정 팀장은 “현장의 기계가 고장이 나서 공장에 가게 되면 비용이 많이 든다. 하지만 사전에 미리 부품을 교체하면 비용이 적게 들고 사고도 안 나는 만큼 2~30억 정도 효과가 있다. 이외에도 정비계획 등을 합해 지속적으로 연간 100억 정도의 경제적 효과가 있다. 물론 (지금보다 시스템을) 정교화할 필요는 있다”라며 “만든 것들을 비지니스화 하면서 해외 제품보다 더 싸게 공급할 수도 있고, 자산들을 쉐어하는 것도 사업화 하고 있다. 지역 중소 IT 기업들과 협업하기도 한다”라고 설명했다.
- 밸류업 가이드라인 최종안 27일 부터 자율공시
- [지역동정] 북한이탈주민 노래경연대회 개최
- 정은보 이사장 “코리아프리미엄 위해 밸류업 적극 지원”
- KT, 멤버십 청년 고객에게 핸드타이드 경험 제공
- LG전자, 기아 전기차 EV3에 웹OS 콘텐츠 공급